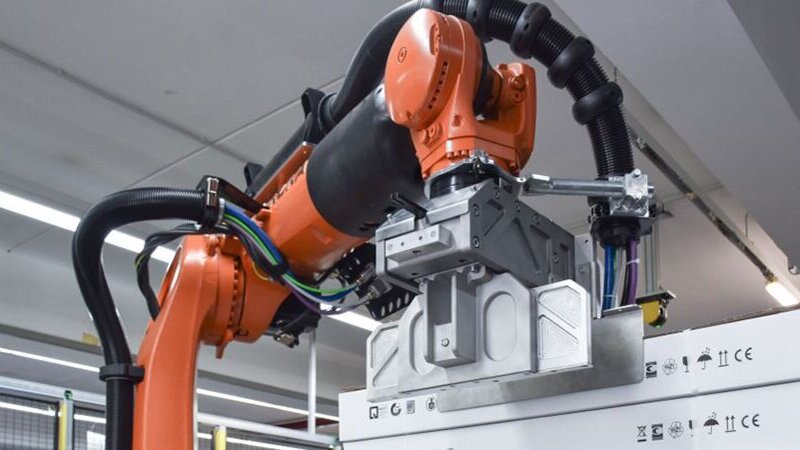
Notre nouvelle machine spéciale attache et empile les motorisations de porte de garage emballées et étiquetées sur des palettes euro ou américaines. Comme ces tâches étaient auparavant effectuées manuellement, l'automatisation se traduit par un processus plus rapide et plus simple et protège la santé de notre main-d'œuvre.
Les pinces du robot ont été développées et en partie installées par nos soins. Pour l'intégration dans le système global, nous sommes partis à la recherche d'un entrepreneur général, et nous en avons trouvé un dans la société HELDELE. HELDELE a planifié, construit et réalisé l'installation conformément à nos exigences et a finalement créé une machine spéciale qui permet une production économe en ressources. Cette coopération a déjà abouti à deux systèmes complets.
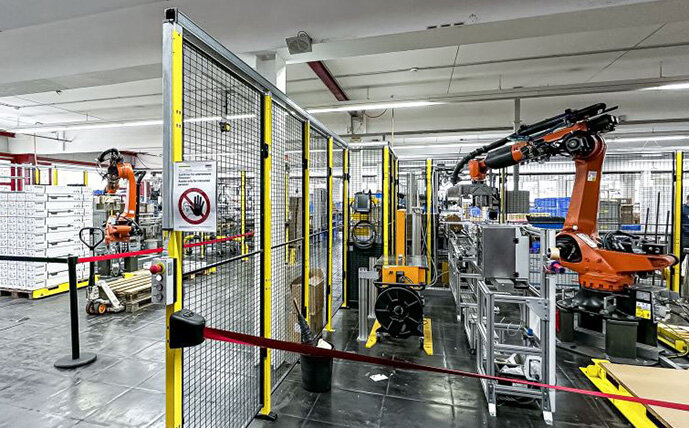
La première station est l'unité de cerclage : le flux de travail du système commence après que les opérateurs ont été emballés dans des cartons. L'employé ajoute tous les composants et accessoires de l'opérateur à la boîte avec l'opérateur de porte de garage et place la boîte sur le convoyeur à rouleaux d'alimentation de l'unité d'alimentation. Un capteur à l'extrémité du convoyeur à rouleaux donne le signal de libération du robot et le robot KUKA atteint la boîte ouverte. Ensuite, la boîte est transportée vers l'unité de cerclage Strapex, où elle est automatiquement fermée et cerclée par une unité de maintien dans la pince. Le robot tourne ensuite la boîte de 180 degrés et l'autre côté est également attaché.
Une connexion à l'ordinateur central est alors établie : le colis est toujours dans le préhenseur du robot et est maintenant transporté vers l'imprimante d'étiquettes de la cabine. Le système complet est connecté à notre ordinateur central, ce qui signifie qu'une plaque signalétique avec toutes les informations souhaitées, par exemple avec notre logo, le numéro de série, les données techniques et un code-barres, est automatiquement produite. Pour assurer une répartition plus uniforme du poids sur les palettes, les colis sont empilés face à face dans des directions alternées. Afin que les étiquettes ne soient toujours visibles que du côté de la commande, l'étiquette est apposée alternativement sur le côté gauche et droit de la boîte.
En fonction des besoins et de la commande, l'employé peut saisir via le logiciel si le colis doit être déposé en position de stockage, sur la palette euro, la palette US ou, alternativement, en position de stockage intermédiaire. La pince s'ouvre d'un côté afin de déposer la caisse. Cela permet de positionner les boîtes très proches les unes des autres. De plus, le préhenseur comprime la rangée en rapprochant les cartons précédents avant d'en déposer un nouveau.
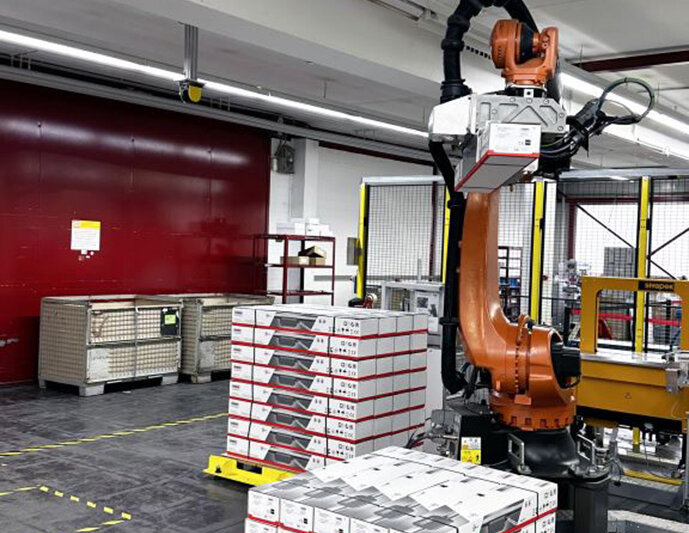
La particularité du système est l'enceinte de sécurité. Pour économiser de l'espace précieux, une clôture de sécurité n'est installée que sur deux côtés. Les deux autres côtés ouverts sont surveillés par des scanners de sécurité. Les deux scanners laser sont montés au plafond et scannent les zones ouvertes du système de robot, assurant ainsi une surveillance continue de la zone dangereuse. Le système s'arrête immédiatement si un scanner détecte un objet ou un mouvement à l'intérieur de la zone dangereuse. Cela permet une utilisation optimale de l'espace supplémentaire gagné lorsque le système n'est pas utilisé, sans qu'une clôture de sécurité fixe ne gêne. De plus, à l'avant de chaque barrière de sécurité, il y a un point de commande avec bouton poussoir d'arrêt d'urgence, bouton de fonctionnement et d'acquittement. Cela permet à l'opérateur de sélectionner différents processus qui arrêtent le système, par exemple lors du changement manuel des palettes lorsque la hauteur d'empilage maximale est atteinte.
L'automatisation de ce processus élimine le besoin d'activités physiquement fatigantes, car une boîte remplie de nos opérateurs pèse jusqu'à 18 kg. Cercler manuellement les deux côtés de la boîte, retourner la boîte, l'étiqueter et empiler le produit final jusqu'à une hauteur de 1,60 cm étaient des tâches ardues pour nos employés. Nous sommes heureux de dire que, grâce à notre nouveau système, ces jours sont révolus.